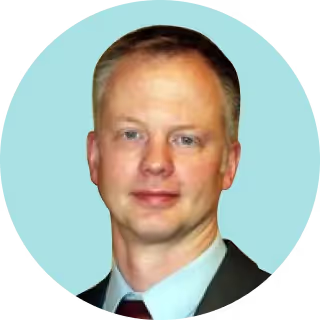
Efficient management of research and production
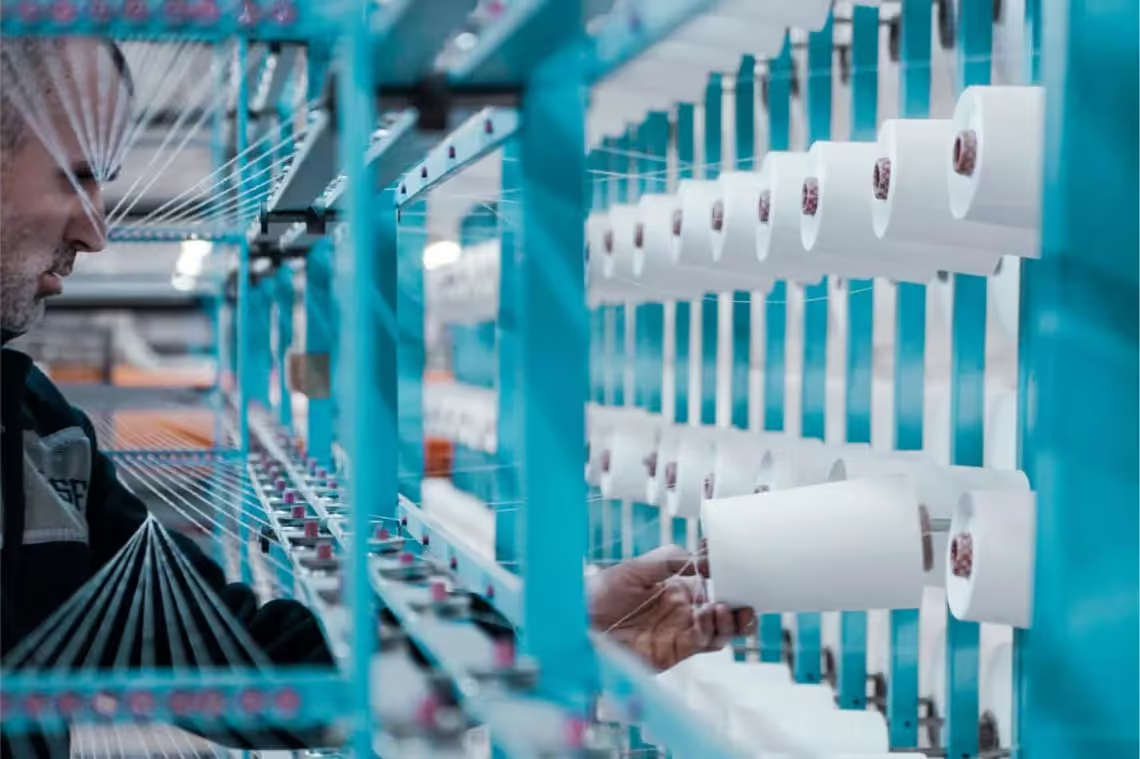
Outsourcing business processes to external service providers has advantages as well as disadvantages. For example, much data is no longer fully available for internal use, which often leads to temporary and stand-alone solutions. With Ninox, this can be prevented.
Customer profile
The Textile Technology Institute of TTI GmbH in Wuppertal has been testing and optimising textile materials for around 90 years. As an expert partner for the fiber and textile industries and mechanical engineering, 26 qualified employees develop modern technical fabrics that are exposed to the highest mechanical loads, for example in the automotive sector and in personal protective clothing.
Challenge
Inefficient temporary arrangements with Excel spreadsheets
In order to be able to carry out important HR and accounting administrative processes professionally and in compliance with the law, even as a smaller company, these areas of responsibility were transferred to external specialists. However, as access to their systems is limited, separate, provisional data collections were also kept, but this was time-consuming and error-prone due to the lack of a uniform system and the lack of multi-user capability of the Excel tables used. Adapting current industry solutions to TTI's individual requirements would have required a great deal of effort, so the decision was made to develop them in-house with Ninox.
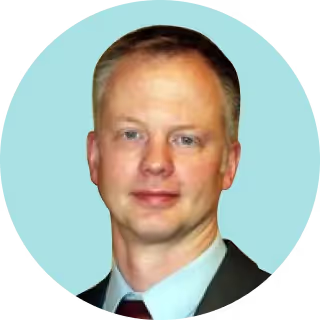
Solution
Central low-code database instead of isolated solutions
The development was carried out in-house under the leadership of a managing director. TTI now manages all research and production orders with Ninox, including commercial and technical processing, tracking and evaluation of production processes using machines and materials, inventory management, deadline and budget monitoring. There are modules for managing customers and invoices as well as suppliers and orders with tracking up to receipt of goods. Employee attendance and absence times are displayed in a calendar and automatically reported to external personnel management. In addition, other company-specific functions for recording maintenance costs and maintaining calibration lists for measuring devices make daily work easier.
Key features
- production control
- Order management
- inventory management
Benefits
Ninox has become an integral part of TTI's day-to-day operations. Where previously various, often local, Excel-based stand-alone solutions required a great deal of effort to find and combine data, today all information is stored in a central database. Whether it's order management, ordering or production control: All parties involved have access to the uniform, always up-to-date data status. TTI is constantly developing the Ninox solution with the aim of representing all databases centrally with one system. The plan also includes involving customers and giving them access to specific information that has been approved for them. In the medium term, Ninox and Xetics LEAN will be used to set up an environment in accordance with Industry 4.0 standards.