On the way to the smart factory: Digitalized production control with Ninox
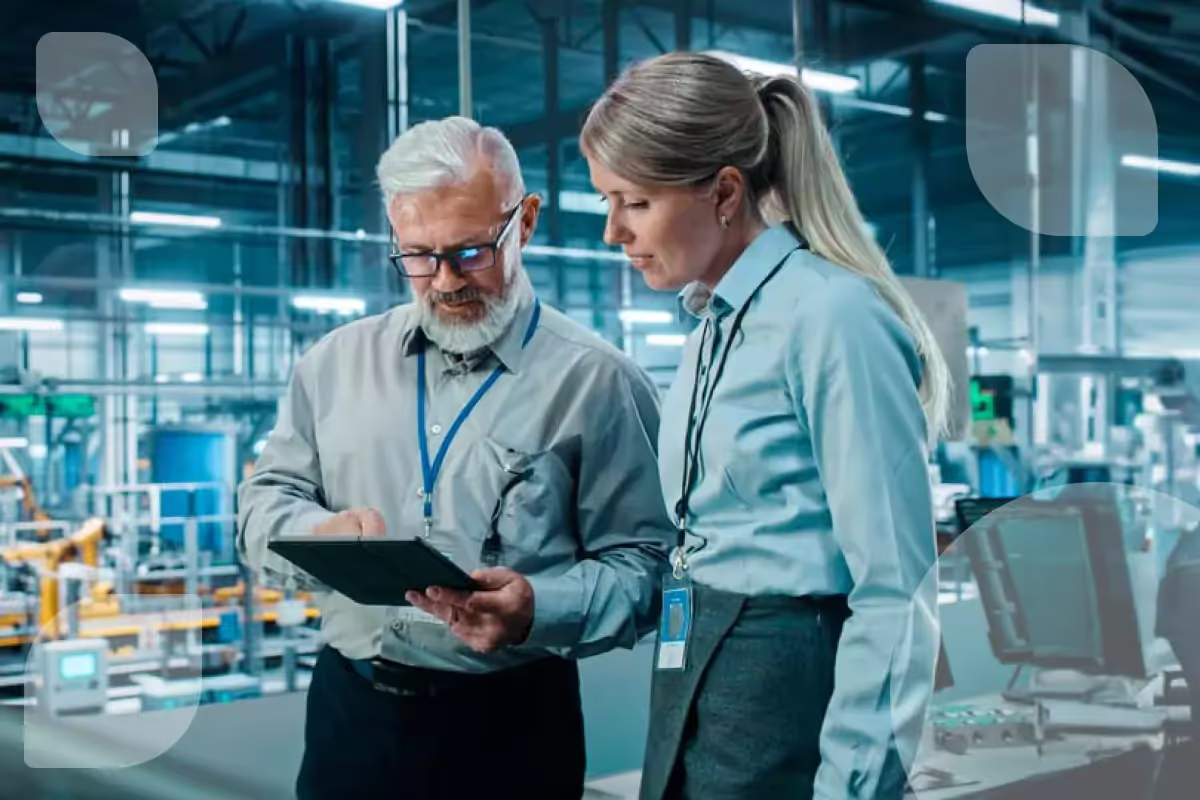
- Definition: What is production control?
- What are the benefits of production control with low-code?
- Smart Factory: stand-alone solutions are a thing of the past
- The four components for automated production: ERP, PPS, MES and APS
- Best practice from the factory
- Conclusion: A central database forms the heart of production control
Expensive industry software and inefficient stand-alone solutions make it difficult for the manufacturing industry to move towards digitalization. There is often a lack of flexible solutions that allow technical adaptations. Low-code systems offer a way out for the industry.
Read this blog post to find out what advantages low-code software offers in production control and what it can look like in practice.
Definition: What is production control?
Production control encompasses all measures and methods used to monitor each individual production phase. Production control combines material and human resources in central planning with the aim of manufacturing a high-quality product. Another aim of production control is to standardize processes and achieve conformity in the manufacturing industry.
What are the benefits of production control with low-code?
Order management is not only becoming increasingly comprehensive in the end customer sector. The manufacturing industry is also faced with constantly growing customer requirements and the desire for individuality. Manual control cannot keep up with this process.
The digitalization of production control ensures a uniform flow of information and offers the possibility of precisely coordinating all phases of production. The problem: conventional ERP systems are often not geared towards changes in production processes. The result is isolated solutions, Excel spreadsheets and manual processes that add to the chaos. One way out is to use low-code platforms such as Ninox, which allow the actual manufacturing processes to be mapped easily and quickly in full, as adjustments are possible.
Companies can implement process changes more quickly and thus adapt and expand their production control quickly and cost-effectively without the need for complex programming. Even employees without an IT background can be integrated into the production control system, which improves collaboration and communication within the company.
Smart Factory: stand-alone solutions are a thing of the past
Excel chaos and handwritten logs in thick folders still characterize the picture in production. This is precisely where digitalization offers enormous advantages. Isolated solutions unnecessarily bloat processes and cost human and financial resources. The heart of the smart factory is therefore a central system from which the entire production control can be organized.
The smart factory describes the networked and automated production of goods. It is important that the production systems can communicate with each other and exchange data. Isolated solutions in which different systems work in isolation from each other have no place in the smart factory. End-to-end networking and integration of all production systems is essential in order to make processes efficient and flexible. For example, machines can communicate with each other and exchange data in order to make automated decisions and optimally control production. An open architecture and standardized interfaces are crucial here.
The four components for automated production: ERP, PPS, MES and APS
The industry needs a software architecture that is both highly specialized and flexible. The most important components include the following systems:
- ERP (Enterprise Resource Planning): ERP systems support the planning and control of resources and business processes.
- PPS (production planning and control): PPS tools enable the planning and control of production processes.
- MES (Manufacturing Execution System): However, the PPS system cannot intervene directly in the production processes; the MES system is required for this. MES systems ensure seamless monitoring of production.
- APS (Advanced Planning and Scheduling): APS systems support the optimized planning of production processes through the analysis of real-time data.
Together, these four components form the basis for intelligent, networked and automated production. However, the basic prerequisite for this is that all four systems can communicate seamlessly with each other.
Best practice from the factory
Tools for production control and order management are often associated with high costs for specialized manufacturing companies. At the same time, there are only a few industry solutions that work just as well for mechanical engineering as they do for metalworking. With low-code platforms such as Ninox, however, you can create your very own production control center - without any in-depth programming knowledge. The following two best practices show what this can look like in practice:
TTI GmbH: Digitizing mechanical engineering and the textile industry
Excel-based isolated solutions, which made it almost impossible to find information and data, determined the everyday life of the textile manufacturing company TTI GmbH (link). As the company's accounting and human resources were outsourced to an external service provider, the medium-sized company relied on Excel to keep track of everything itself. However, the opposite was the case. Complicated processes and error-prone data collections quickly became a success killer. Thanks to the use of Ninox, however, production control, order management and merchandise management could be brought together in a central system.
Conclusion: A central database forms the heart of production control
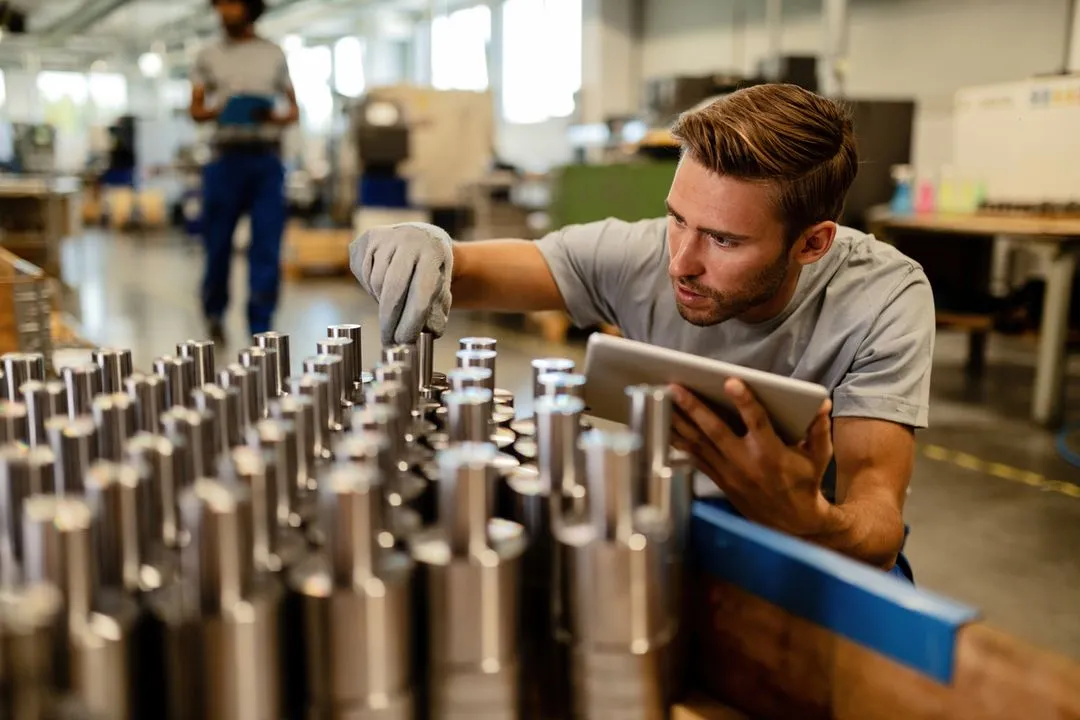
The modern production control of manufacturing companies can be implemented particularly efficiently with low-code platforms. Probably the greatest advantage of low-code systems is their flexibility and simultaneous specialization. This means that companies from a wide variety of sectors can use one tool and adapt it to their own production process. As a central point of contact, a low-code database replaces isolated stand-alone solutions and thus creates a more efficient path for the digital factory.