Retail & consumer goods
Technical service in food production
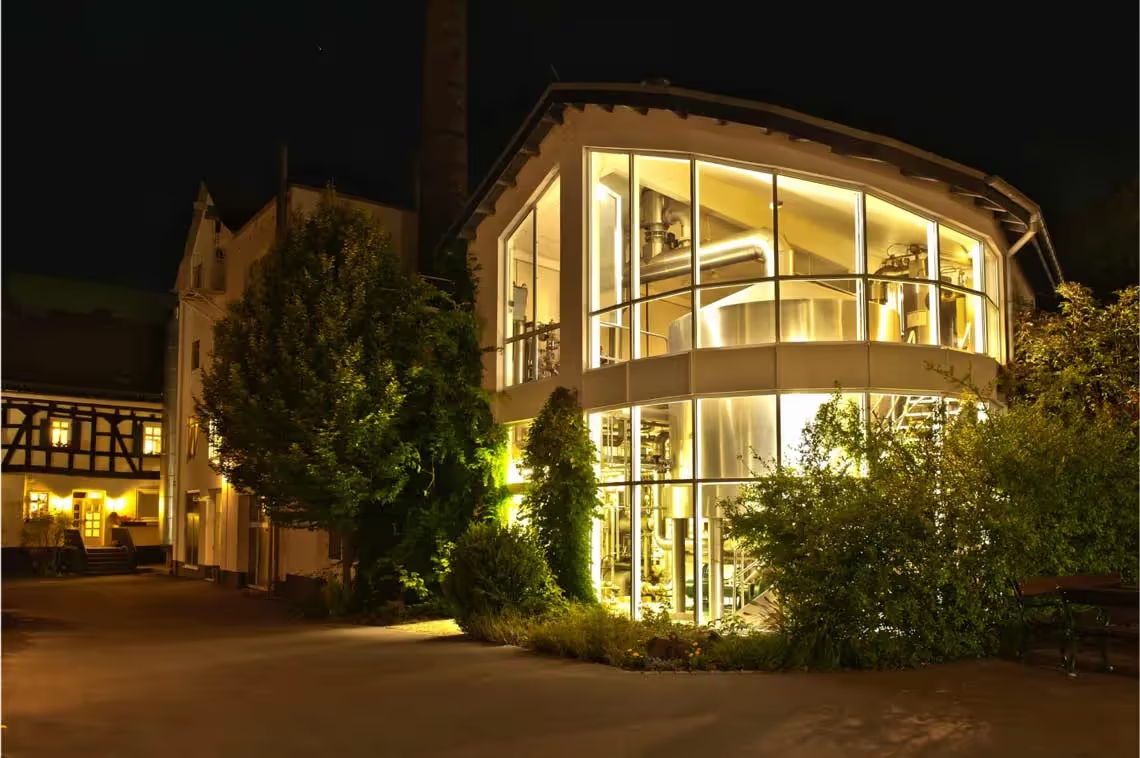
A so-called purity law applies not only to ingredients used in beer brewing, but also to the production facilities. In order to implement the strict hygiene regulations of food law as closely as possible, the Westerwald Brewery organises and documents all processes with Ninox.
Customer profile
The name "Hachenburger" has stood for high-quality beer specialities since 1861. The Westerwald brewery is one of the oldest Pils breweries in Germany and is still an independent family business, now in its fifth generation. Roughly 90 employees produce about 70,000 hectolitres of beer specialities and beer-based mixed drinks every year. The beer is brewed exclusively with aroma hops, some of which are home-grown.
Challenge
Processes with paper forms and Excel spreadsheets
Hachenburger is a traditional, but also thoroughly modern company. Software solutions have long existed for accounting and some brewery-specific standard processes, but not for the numerous individual processes at Hachenburger. Repairs, maintenance, and cleaning of technical equipment must be well organised, controlled, and documented as part of quality assurance. For this purpose, numerous paper forms and Excel tables were used. In the search for a digital form solution that would make the job easier, Hachenburger came across Ninox and discovered that it could do so much more.
Solution
Boosted efficiency through digitalised processes
Within a few weeks, a senior technical employee at Hachenburger had developed a solution with Ninox that almost completely replaced paper forms and Excel spreadsheets and streamlined processes. The employees concerned now scan the barcodes of the components and work through their checklists with iPads. All data is immediately available in a centralised location and no longer needs to be transferred. Repair lists, daily reports, and inspection records can be accessed at the touch of a button, and the error rate has been significantly reduced.
Long familiarisation periods or extensive staff training were not necessary. Hachenburger uses Ninox Cloud with various personal computers in the administration and several iPads in the brewery.
Key Features
- Central data storage
- Mobile barcode use
- Automated documentation
Benefits
The initial problem at Hachenburger, the improvement of processes in maintenance and quality assurance, was quickly solved with Ninox. The corresponding modules were also tested and recognised as part of the IFS Food and Slow Brew certification. They are further developed as required and now also include, among other things, an evaluation system of the premium key figures for the technical staff.
However, the ease with which individual solutions can be developed has also aroused interest in other departments. In the meantime, Ninox is also used for tasks in the areas of merchandise management, logistics, personnel and project management as well as visitor management. Further ideas are available and are being implemented bit by bit. The approaching goal is to create an integrated corporate solution with Ninox.